5 Simple Techniques For Alcast Company
5 Simple Techniques For Alcast Company
Blog Article
3 Easy Facts About Alcast Company Explained
Table of ContentsThings about Alcast CompanyThings about Alcast CompanyA Biased View of Alcast CompanyThe Ultimate Guide To Alcast CompanyExcitement About Alcast CompanyThe Only Guide to Alcast Company
Chemical Comparison of Cast Light weight aluminum Alloys Silicon promotes castability by decreasing the alloy's melting temperature level and enhancing fluidness throughout spreading. Additionally, silicon adds to the alloy's stamina and put on resistance, making it important in applications where resilience is essential, such as auto parts and engine parts.It likewise improves the machinability of the alloy, making it easier to process into ended up products. This way, iron adds to the overall workability of light weight aluminum alloys. Copper increases electrical conductivity, making it useful in electric applications. It additionally boosts deterioration resistance and includes in the alloy's total strength.
Manganese contributes to the strength of aluminum alloys and boosts workability. Magnesium is a lightweight component that gives toughness and impact resistance to aluminum alloys.
The Best Strategy To Use For Alcast Company
It allows the production of lightweight elements with superb mechanical homes. Zinc improves the castability of light weight aluminum alloys and aids regulate the solidification process during casting. It improves the alloy's stamina and firmness. It is usually found in applications where elaborate shapes and fine details are needed, such as attractive spreadings and particular automotive parts.
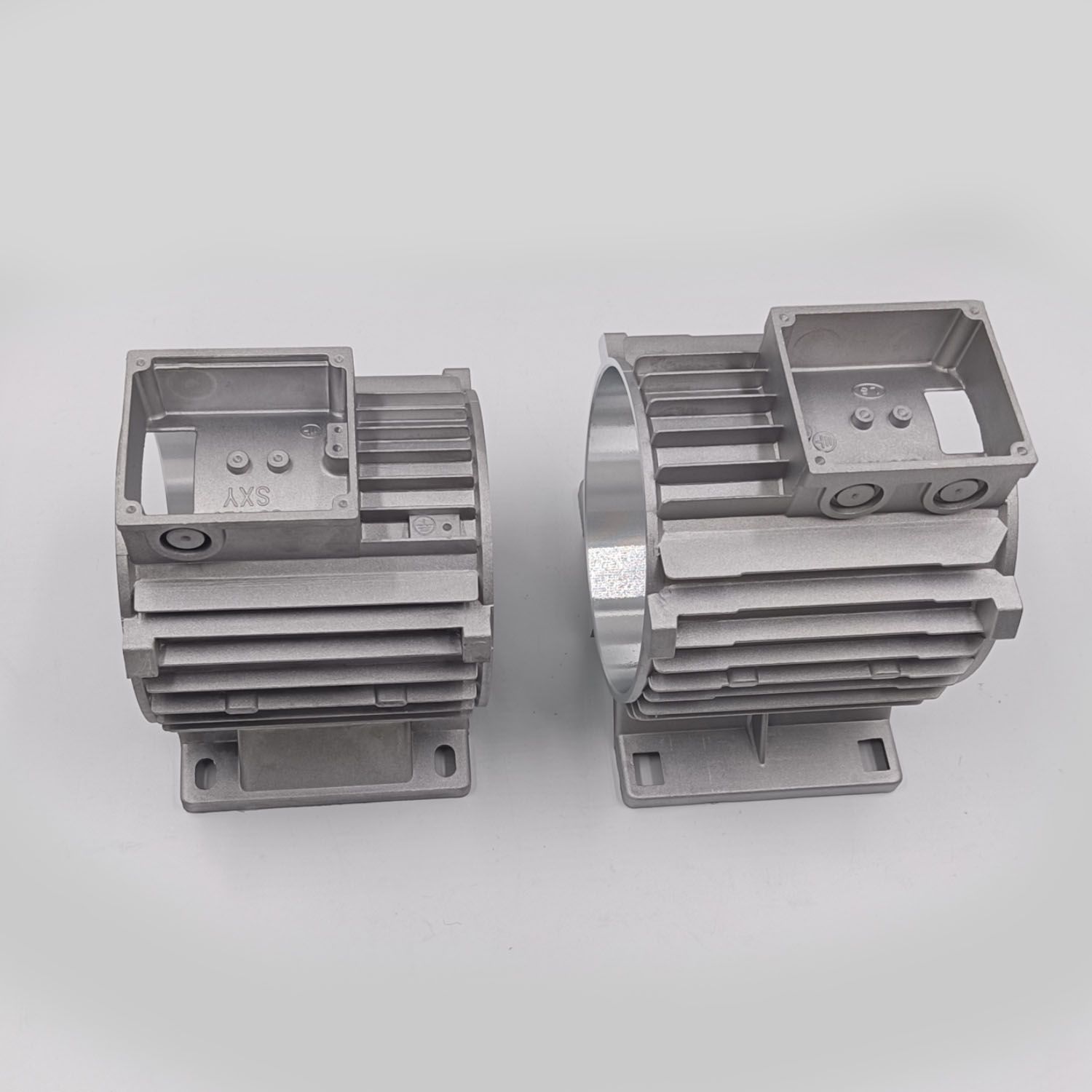
The primary thermal conductivity, tensile strength, yield strength, and elongation vary. Amongst the above alloys, A356 has the greatest thermal conductivity, and A380 and ADC12 have the cheapest.
How Alcast Company can Save You Time, Stress, and Money.

In accuracy casting, 6063 is appropriate for applications where intricate geometries and high-quality surface coatings are paramount. Examples consist of telecommunication enclosures, where the alloy's exceptional formability enables sleek and visually pleasing layouts while keeping structural honesty. In a similar way, in the Illumination Solutions sector, precision-cast 6063 components create sophisticated and reliable lighting fixtures that require complex forms and excellent thermal efficiency.
It results in a better surface area coating and much better deterioration resistance in A360. The A360 displays exceptional elongation, making it optimal for complicated and thin-walled elements. In precision casting applications, A360 is well-suited for industries such as Consumer Electronics, Telecommunication, and Power Tools. Its improved fluidity permits elaborate, high-precision components like smartphone casings and interaction tool real estates.
8 Simple Techniques For Alcast Company
Its one-of-a-kind homes make A360 a useful selection for accuracy spreading in these sectors, boosting item longevity and quality. Casting Foundry. Aluminum alloy 380, or A380, is a widely made use of spreading alloy with numerous unique attributes.
In accuracy casting, light weight aluminum 413 radiates in the Customer Electronic Devices and Power helpful resources Tools sectors. This alloy's remarkable rust resistance makes it an excellent selection for outside applications, guaranteeing durable, long lasting products in the stated sectors.
The Main Principles Of Alcast Company
The aluminum alloy you choose will significantly affect both the spreading procedure and the properties of the final product. Because of this, you should make your decision very carefully and take an educated technique.
Determining the most appropriate aluminum alloy for your application will mean evaluating a large selection of attributes. The very first category addresses alloy characteristics that influence the manufacturing process.
What Does Alcast Company Mean?
The alloy you pick for die casting straight affects a number of aspects of the spreading procedure, like how very easy the alloy is to deal with and if it is vulnerable to casting problems. Warm breaking, likewise referred to as solidification fracturing, is a normal die casting defect for aluminum alloys that can cause internal or surface-level tears or splits.
Specific aluminum alloys are extra prone to hot breaking than others, and your selection needs to consider this. An additional usual defect discovered in the die spreading of aluminum is pass away soldering, which is when the cast sticks to the die wall surfaces and makes ejection difficult. It can damage both the cast and the die, so you need to seek alloys with high anti-soldering buildings.
Corrosion resistance, which is currently a remarkable characteristic of aluminum, can differ substantially from alloy to alloy and is a vital particular to think about relying on the ecological problems your product will be exposed to (aluminum casting manufacturer). Put on resistance is an additional property commonly looked for in aluminum items and can separate some alloys
Report this page